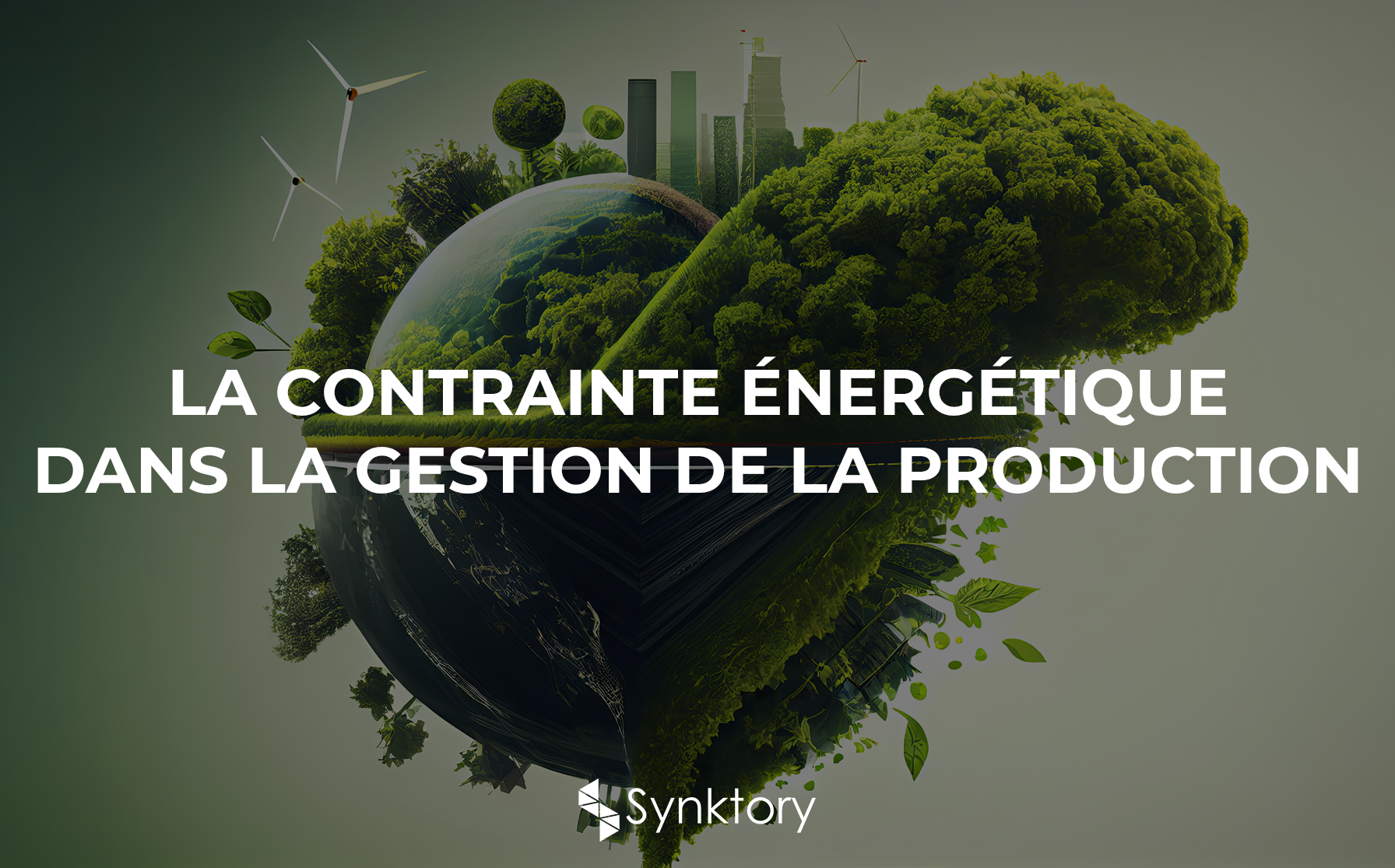
La contrainte énergétique dans la gestion de la production
La consommation énergétique dans une chaîne de production devient toujours plus primordiale. En effet, l'énergie représente un coût très important sur une chaîne de production, exacerbée ces derniers mois avec l'évolution importante du coût du gaz et de l'électricité augmentant de 47 % entre 2021 et 2024 selon une étude de l'INSEE. En complément, la conscience environnementale, confirmée par l'agenda 2030 fixé par les membres de l'ONU, concentre l'attention des responsables des chaînes de production.
La prise en compte de cette dimension dans l'organisation des usines ou ateliers et l'ordonnancement des travaux permet non seulement de réduire les coûts énergétiques, mais aussi d'améliorer l'efficacité de la production en répondant aux attentes en matière de développement durable.
La prise en compte de la consommation énergétique
En optimisant l'utilisation de l'énergie, les entreprises peuvent :
- Réduire leurs coûts opérationnels ; une gestion efficace de l'énergie peut conduire à des économies substantielles, surtout dans des secteurs à forte intensité énergétique.
- Contribuer à la durabilité environnementale ; la réduction de la consommation d'énergie entraîne une diminution des émissions de gaz à effet de serre, contribuant ainsi aux objectifs de durabilité.
- Améliorer la compétitivité ; la réduction des dépenses énergétiques permet d'alléger les coûts de production, rendant les produits plus compétitifs sur des marchés toujours plus concurrentiels.
L'intégration de la consommation énergétique dans l'ordonnancement
L'ordonnancement des tâches dans un atelier peut être optimisé en intégrant différents critères identifiant l'impact énergétique de leur réalisation. Ce critère énergétique peut donc découler de plusieurs origines : le temps machine et sa consommation énergétique, la nature des matières premières nécessitant l'utilisation de machine spécifique à forte consommation, etc. Ce critère énergétique sera donc un élément de priorisation complémentaire à l'ordonnancement déjà appliqué qui s'articule principalement sur le temps de production, l'échéance de livraison client et la disponibilité des matières premières ou des postes de travail.
Chaque poste de travail ou machine possède un profil énergétique spécifique. En analysant ces profils, il est possible de planifier les opérations en fonction des moments où les tarifs d'énergie sont les plus bas, concentrer leur utilisation sur une période spécifique pour éviter une marche permanente donc une consommation « inutile » en veille.
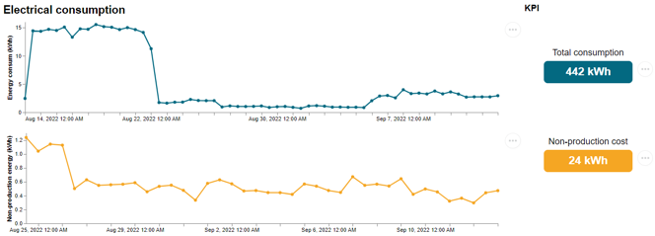
Graphique de la société InUse démontrant la surconsommation électrique en état de non-production durant laquelle la machine reste allumée par exemple. Lien vers l’étude : https://inuse.eu/fr/blog/surconsommation-energetique-flux-process/
Par ailleurs, la manipulation de certaines matières sera plus consommatrice d'énergie que d'autres. Il convient donc d'identifier celle-ci pour prendre en compte son critère énergétique dans l'ordonnancement. En effet, le façonnage d'une pièce métallique nécessitera plus de puissance machine en fonction de l'épaisseur de la matière, et donc d'énergie et ce même si le temps machine (presse par exemple) est identique. L'identification de ces matières premières est donc à ajouter au profil énergétique précité.
La technologie pour la définition du profil énergétique
Les fournisseurs d'énergie proposent de surveiller et de contrôler la consommation en temps réel. Ils peuvent donc être utilisés pour mesurer la consommation des différents postes de travail particulièrement si les machine en place sont assez anciennes.
Les capteurs intelligents connectés (iIoT) peuvent également fournir des données en temps réel sur la consommation énergétique des équipements. Ces dispositifs ne nécessitent pas systématiquement des machines de dernière génération et peuvent s'implanter au sein de la chaîne de production pour participer à cette mesure.
La récolte de ces informations sera un préalable à l'exploitation de l'IA pour analyser les données de consommation énergétique et proposer des améliorations dans l'ordonnancement. L'exploitation de l'IA sera réalisée dans un second temps lorsque le volume de données acquis permettra d'exploiter des modèles d'apprentissage de la consommation énergétique et suggérer alors des ajustements de production. Des solutions comme KomboX peuvent centraliser ces données et apporterdes analyses complexes de situations monitorées en production. Ceux –ci une fois remonté au logiciel de production, permettrait d'optimiser la consommation des machines en temps réel.
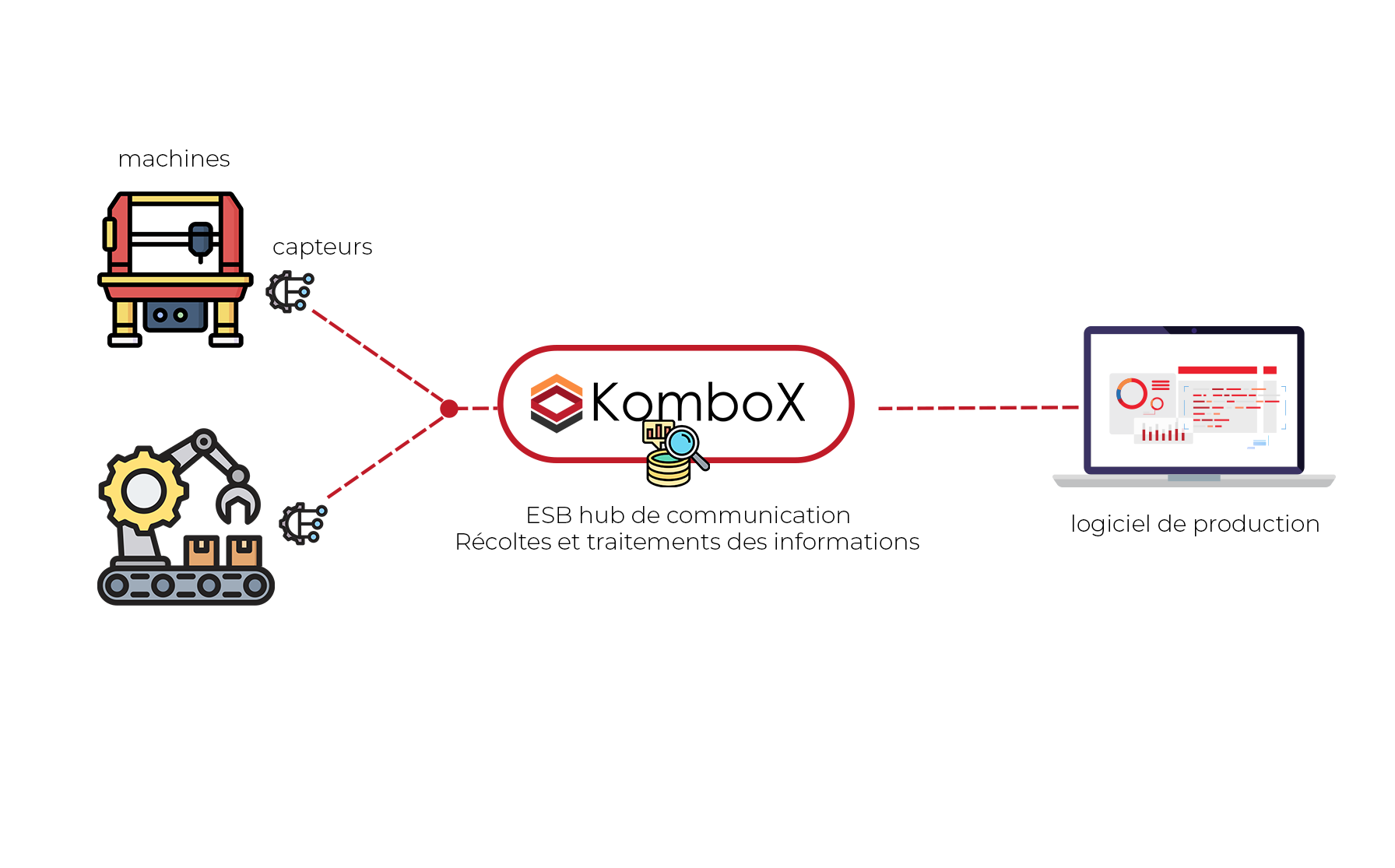
Conclusion
L'optimisation énergétique doit se faire en différentes phases :
- Acter une stratégie de réduction des coûts énergétiques,
- Partager l'objectif avec les différents acteurs de la production et accepter les changements nécessaires, (pourquoi ne pas partager cet objectif à ses clients)
- Mesurer les différentes consommations,
- Définir le profil énergétique des postes et des matières premières,
- Définit le critère énergétique et son échelle,
- Appliquer ce critère dans l'ordonnancement de sa production,
- Mesurer les gains sur une période suffisamment révélatrice.
Il n'est pas nécessaire d'avoir des machines de dernière génération pour s'engager dans cette démarche car elle peut être portée dans un premier temps avec les équipements en place et des investissements minimes, essentiellement concentrée sur l'organisation de la production et des bons réflexes.
En appliquant des méthodes d'optimisation de l'énergie, les entreprises peuvent non seulement réduire leurs coûts énergétiques mais aussi s'inscrire dans une démarche de production plus durable avec l'engagement actif de son personnel.